Dental-office Renovations Highlight Changing Protocols, Technology
Filling Today’s Needs
By Mark Morris
When Craig Sweitzer built his first dental office 37 years ago, he thought it was the coolest thing he had ever done.
As owners of Sweitzer Construction, Craig and his wife, Pat, enjoyed learning the unique design requirements and the technical knowledge required to build dental suites, known as operatories.
“We like to work on projects that are new, fresh, and exciting,” Sweitzer said. “Dental offices fit that bill because dental technology is evolving, and it’s fun to stay current with it.”
In a recent string of projects, the Sweitzers’ firm built or renovated three dental practices in the Berkshires, all owned by women dentists. Berkshire Dental Arts and Berkshire Dentistry, both in Pittsfield, and Shire City Endo in Lenox all presented different challenges to the team, among them building dental practices during a pandemic.
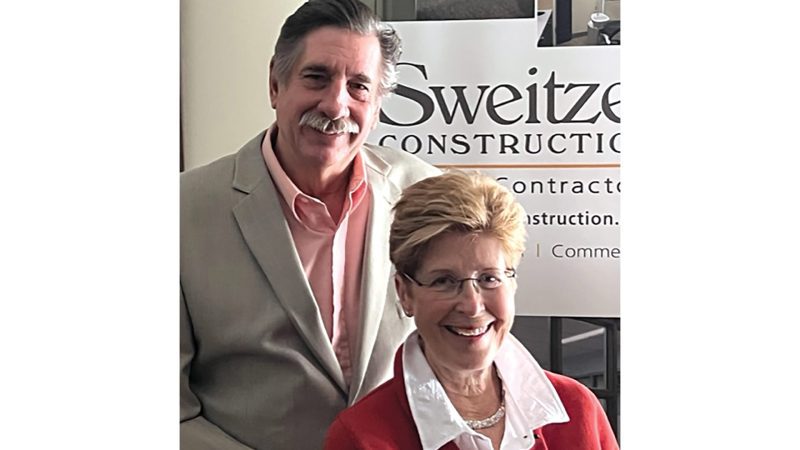
Dr. Sarah Martinelli said the building where her practice, Shire City Endo, does business began as a “rectangular brick box.” Built in 1978, three different banks occupied the site before Martinelli purchased the building in February 2020. Having worked in the area, she knew that dentists referred patients for endodontic work from all over the region, so the central location of this building on Route 7 in Lenox made it an ideal spot.
Craig Sweitzer explained that, when dentists plan a renovation or construction project, they will meet with him early in the process. From the choice of equipment to how each room lays out, together they form a plan.
“There are lots of decisions to be made,” he said, “from where the plumbing and electrical lines go to whether the doctor is right-handed or left, and do they want cuspidors or just suction?”
A dental-equipment supplier also enters the picture early on to work in partnership with the construction crew and the dentist.
“We do all the underground, behind-the-wall, and under-floor infrastructure work to make sure it will accommodate the specialized equipment the doctor ordered,” Sweitzer said.
Dental offices fit that bill because dental technology is evolving, and it’s fun to stay current with it.”
For Shire City Endo, part of the early work involved removing a drive-up window left over from the banking days. When the crew was drilling into the foundation to run plumbing and electrical lines, they ran into another legacy of the building’s former use.
Foundation floors in banks are usually much thicker than those in regular commercial buildings to deter would-be thieves from tunneling in from underneath. After much more effort, the crew was able to install the necessary lines in the right places.
“I wasn’t worried before about someone tunneling into my practice,” Martinelli said jokingly. “And I sleep well at night knowing I’m protected from that now.”
The thick floors didn’t slow down the project too much, but as Pat Sweitzer noted, coordinating schedules with the medical supplier is an important part of the process. “The whole project is orchestrated for our crews to finish their work just as the medical equipment and the installers are available.”
As a general contractor, Sweitzer Construction is well-acquainted with the difficulties of sticking to schedules during the pandemic, not to mention recent price increases for raw materials. Lumber is the most notable building material to see wild price increases of up to 250%. Craig said he does not use much lumber, but instead uses steel studs to frame walls in his commercial projects. Still, he noted that steel has begun catching up to lumber in price and difficulty to get when it’s needed.
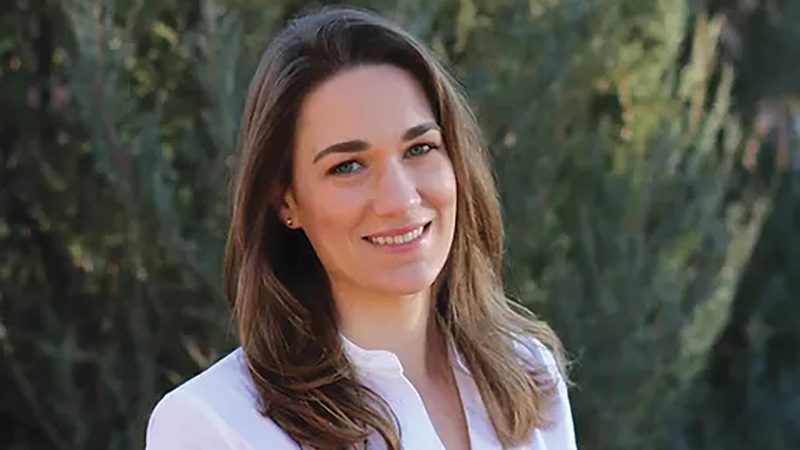
“We order materials long before we need them and then hope they arrive somewhere around the time we are ready to use them,” he explained. “It takes our office staff much more effort to make sure materials get here on time.”
Go with the Flow
When the pandemic first hit, air flow inside buildings suddenly became an essential consideration, especially in healthcare facilities. Sweitzer and the HVAC subcontractors who work with his company began to study how to design new systems and retrofit old ones to keep everyone safe.
Whether COVID-19 had existed or not, Martinelli knew she would have to replace the entire HVAC system in her building. Sweitzer and Mark Edwards from M&E Mechanical Contractors, the HVAC subcontractor for the project, installed a state-of-the-art negative-air system for all the operatories at Shire City Endo. Sweitzer explained it as a system that captures pathogens in the air which are immediately pulled out of the room by an exhaust fan before they can spread. In the past, operatories often had exhaust vents in the ceiling. The standard now is to locate these lower on the wall.
“Dentists and hygienists work in people’s mouths, the main path of respiration,” he said. “With lower vents, any pathogens are directed down to the floor instead of into the provider’s face.”
Martinelli appreciated that she had the opportunity to install a new HVAC system to deal with COVID and any other airborne maladies. At the same time, she saw her colleagues struggle to find answers on how to retrofit their offices to mitigate risks and improve air quality.
By purchasing this unit, it saved us from ripping out the ceiling and replacing the entire ventilation system. That would have been absolutely disruptive.”
Because Sweitzer and Edwards had been so helpful to her, Martinelli coordinated a Zoom call with the contractors and the Berkshire Dental Society, so dentists could get answers on how to manage air ventilation in their practices.
“Craig and Mark were great resources to the entire dental community, who had plenty of questions on how to keep their patients and staff safe,” she said.
Pat Sweitzer was on the Zoom call and credited Martinelli for organizing it. “The dentists had done lots of research, and we had done lots of research,” Pat said. “It was a time when everyone was learning how to contain COVID through different HVAC systems.”
Dr. Anne Barnes, who runs Berkshire Dental Arts, is one of the dentists who chose to retrofit her office with an air purifier that turns over the air in the entire room in three minutes. She said it does an excellent job, and while it’s a large piece of equipment in the corner of the room, it beats the alternative.
“By purchasing this unit, it saved us from ripping out the ceiling and replacing the entire ventilation system,” she said. “That would have been absolutely disruptive.”
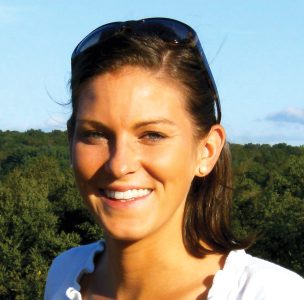
In 2018, Barnes established Berkshire Dental Arts after assuming Dr. Neil Pyser’s practice located on South Street in Pittsfield. The building was constructed in the 1960s by four dentists, and while it has changed hands several times over the years, the interior space was not much different from when it was first designed.
“What was here just didn’t work for me and wasn’t planned out for today’s dentistry,” Barnes said. As a captain in the U.S. Army Dental Corps, she had access to all the latest equipment, so while she knew what she wanted, the challenge was how to fit it in a predefined space.
At Martinelli’s recommendation, Barnes asked Sweitzer for help on how to make better use of the defined footprint of the building.
“Craig helped me troubleshoot and think about ways to convert the space we have into something more efficient,” she said. Her practice consists of four operatories, two used by Barnes, with hygienists working in the other two rooms.
She and her husband, Charles, who is also the practice manager, had a mental picture of how the operatories should look, but admitted they didn’t have the expertise on how to bring in new equipment without sacrificing elbow room.
“I wanted to make each room functional and comfortable to work in,” Barnes said. “Craig knows how much space you need around the chair and where to place all the plumbing and electrical hookups we use.”
She enjoys her redesigned office because she now has the equipment to do 90% of her lab work in house instead of sending it to an outside firm. For example, if a patient wanted to change the color of a crown, they would normally have to make an appointment two weeks after their visit while the crown goes to a lab. Because Barnes now has a ceramic oven in her office, the patient needs to wait just 15 minutes for the adjustment.
“A ceramic oven is a small piece of equipment,” she said, “but if you don’t have the counter space for it, you’re out of luck.”
Martinelli was also pleased with her office renovation, noting that she appreciated Sweitzer’s strong knowledge of dental-building infrastructure.
“In addition to knowing all the building codes that pertain to dental-treatment rooms, he also knows how to navigate the whole permitting process,” she said. “And he knew what needed to be done to check all the boxes at the end of the job.”
Tooth of the Matter
The knowledge the Sweitzers acquired to build dental offices has allowed his company to expand into other highly technical projects. From photovoltaic solar work to building clean rooms for high-tech companies, their business keeps expanding. Even with the new areas of focus, though, Craig still enjoys dental-office construction.
“Dentistry keeps changing, and there are always technical parts to it,” he said. “Besides, it’s more fun than building someone a closet.”