Mercy Medical Takes a Six Sigma Approach to Healthcare
By GEORGE O’BRIEN
The sign on the door says ‘Mission Control.’
That’s a play on words, obviously. There’s a definite nod to NASA and its famous control room, where decisions were made, and moonshots were choregraphed. But that word ‘mission’ takes on a different, higher meaning at Mercy Medical Center, part of Trinity Health Of New England. The hospital was founded more than 125 years ago by the Sisters of Providence, and its mission to care for the region’s population, and especially those who are traditionally underserved, has been paramount and in most ways more important than the bottom line.
But these days, the mission is being carried out in a different way, said Mark Fulco, president and CEO at Mercy, who recently marked a year at the helm. He noted that, in many ways, the hospital, and the Trinity system on the whole, are taking cues from the auto industry and other business sectors and taking a Six Sigma approach to healthcare — a lean approach, one that manifests itself in a number of ways.
But the major focus is on making the medical center more efficient in ways that will reduce costs without sacrificing quality.
“It’s been a watershed for us, because it has changed our work and has helped us focus on key metrics to drive efficiencies,” said Fulco, adding that the hospital’s efforts to become leaner are reflected in everything from reduced wait times in the ER to an increase in the number of discharges over last year by staffing up more beds; from reducing the overall cost of each discharge by roughly $1,100 to cutting back on travel by using videoconferencing technology.
Overall, Mercy and the Trinity system are eliminating waste whenever possible, creating efficiencies in every department, and constantly looking for ways to improve service without impacting quality of service.
This work extends all the way down to the medical center’s printers and copiers, the number of which has declined noticeably over the past year or so.
“We’ve gone very much paperless,” Fulco explained. “We had two big meetings this morning, and instead of printing out huge packets of information, we did it electronically and on large monitors.
“It’s unbelievable what a color copy costs these days, and when you produce lots of color copies with charts and graphs, it costs a lot of money,” he went on. “So we’ve actually taken printers away and put codes on some of our printers so departments are accounting for every color copy they make.”
This focus on lean practices and accountability brings us back to the room behind the door bearing the sign that says ‘Mission Control’ and its co-called ACE (achieving clinical excellence) boards that track progress in specific areas.
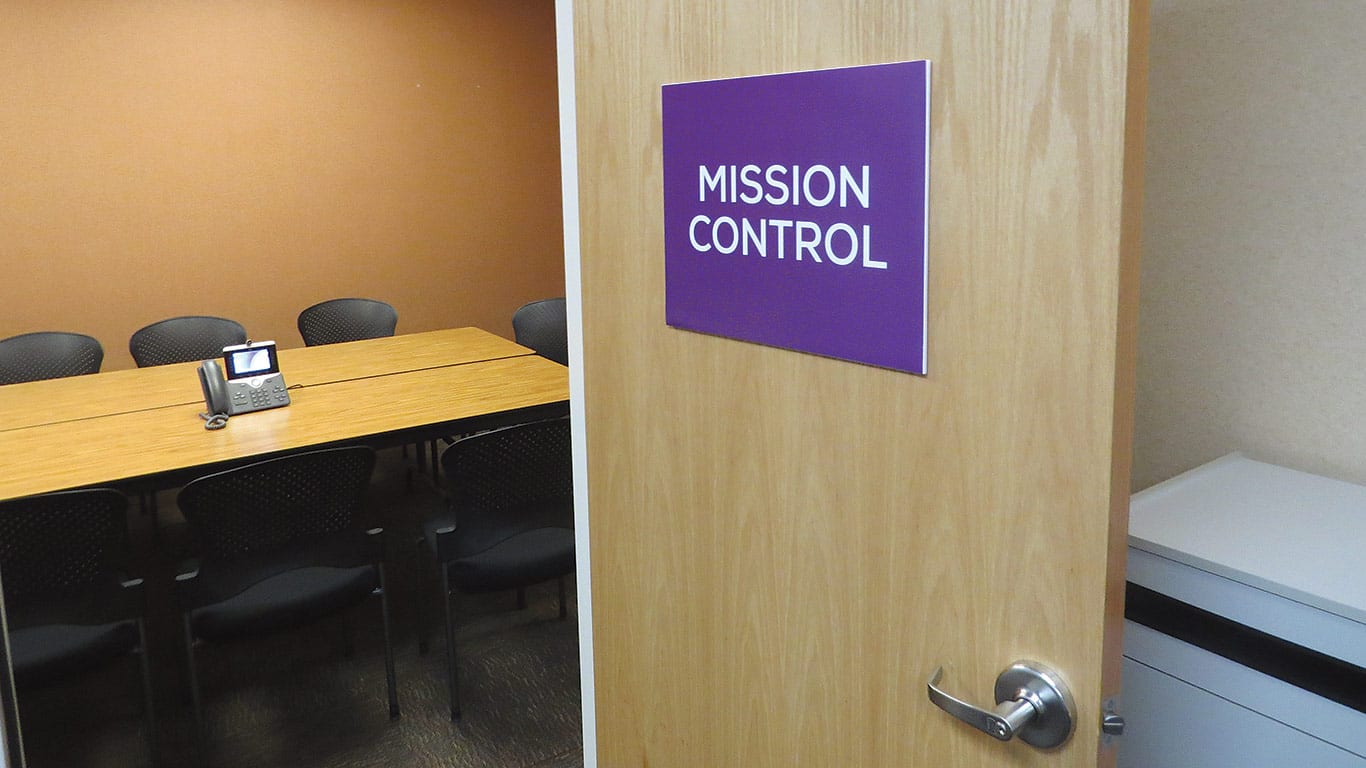
They are part of what is now known as the Trinity Health Management System, or lean daily management, an operating philosophy, if you will, that we’ll explore in greater detail later.
It also brings us to the large conference room, also known as the Patient Safety and Flow Room, a few hundred paces away. Here, each day at 8 a.m. (no one is typically late, because if they are, they have to walk into a room filled with people who were on time), as many as 50 people gather for what are known as ‘huddles.’
These are strategy sessions where issues are discussed, problems are identified, and solutions generated, said Fulco, who offered an example.
“We have several huddles every morning, and one of them is our ‘tier 3 huddle,’ where we bring together leaders from across the entire hospital,” he explained. “The very first thing we talk about is patient safety or problems that came up the night before, or safety catches — like if something was a near-miss — because we want to know, first and foremost, what we need to do to be better and keep patients safer.
“That’s our early-warning system,” he went on. “And at the meeting, if we have a detected infection, we report it, and then we talk about what we can do to prevent another case like that from happening.”
For this issue, HCN looks at Mercy’s broad efforts to employ the principles of Six Sigma and become, in keeping with its mission, lean but certainly not mean, at least in a very literal sense.
Work in Progress
They’re calling it the ‘29-minute pledge.’
That number is significant because of its specificity, meaning it’s not the ‘30-minute pledge,’ a much rounder number to be sure.
It refers to the maximum time it will take for someone visiting Mercy’s Emergency Department to see a physician or physician’s asistant, and this pledge is due to be launched in the coming weeks and announced with billboards and other forms of advertising.
“We’re pledging a door-to-provider time, in our emergency room, of 29 minutes,” Fulco explained, adding that the program has essentially been rolled out already, but the billboards won’t be going up for another few weeks. “We chose 29 minutes because it represents an average of what we can hold out as a pledge; there are times when we’ve averaged 16 minutes.”
The 29-minute pledge is a another example of Mercy’s efforts to improve quality of service while also becoming more efficient and taking cost out of the equation, said Fulco, noting that it is one of many initiatives put in place during what has been a very intriguing and challenging (he would use that word early and quite often, and usually with at least one ‘really’ in front of it) first year at the helm — and year for all those who provide healthcare.
He would sum it all up, sort of, by saying, “I knew what I was getting into — I knew it was challenging; it’s just been more work than I expected — not in a bad way, but in a good way, because it’s been a labor of love.”
What he was getting into is a very demanding climate for not just Mercy but all healthcare providers, one in which reimbursements for services provided, especially from public payers including Medicaid and Medicare, do not really come close to covering the cost of those services.
This disparity is especially large in the broad realm of behavioral health, Fulco noted, adding quickly that, through its facilities at Providence Behavioral Health Hospital, the Trinity Health system is the region’s leading provider of such services.
And these are services that are, from a purely bottom-line perspective, losing propositions, again because the cost of care is not being met by those paying for it. And while Providence and the Trinity system have always been mission-driven, there comes a point where the losses being incurred cannot be sustained, said Fulco, adding that this reality explains why there were inevitable cutbacks at Providence, and in other departments under the Mercy/Trinity umbrella as well.
“We had to make some tough decisions — the status quo simply doesn’t work,” he explained, adding that among these decisions were staffing reductions at Providence (most employees were offered other positions within the system) and cutbacks within or elimination of some departments at Mercy, including the Hearing Center.
While the cutbacks and staff reductions garnered the largest headlines regarding the Mercy system in 2018, a considerable amount of work going on behind the scenes to make the system more efficient, more responsive, and, yes, leaner — efforts like the 29-minute pledge — were perhaps more newsworthy.
As he talked about them, Fulco said these initiatives accurately reflect a system-wide operating philosophy being implemented by Trinity Health Of New England’s recently appointed CEO, Dr. Reginald Eddy, a former emergency-room physician.
“He really gets it,” said Fulco. “He gets it from a care perspective, and he has a strong sense of urgency that he’s really instilled in us in terms of doing it right, doing it well, and doing it quick, not just from a patient perspective, but from a business sense.”
Tracking Improvement
As he talked about the Trinity Health Management System, Fulco said it is focused on quality metrics, or what he called ‘people-centered metrics,’ which are carefully monitored with an eye toward continuous improvement.
As an example, he cited the infection rate, a key issue — and major challenge — for all hospitals.
“Our infection rate has remained below target and below what’s expected for a hospital like Mercy, and is, in fact, one of the 20 lowest infection rates across all the 94 or 95 Trinity hospitals,” he said, using infections from urinary catheters as an example of how Mercy tracks issues and addresses problems.
Steps such as these have a trackable impact on quality, as measured in a number of ways and by a number of entities, said Fulco, noting that Mercy’s Leapfrog score — its rating based on surveys undertaken by the Washington, D.C.-based Leapfrog Group, improved from ‘C’ to ‘B’ in 2018.
“Our goal is to be an ‘A,’ and we’re not stopping until we get there, and then we have to stay there, which becomes progressively more difficult,” he explained. “But we’ve improved by one whole grade, which is a significant step forward.”
But while quality is certainly an important benchmark, so too is cost, said Fulco, adding that the ultimate goal is to not only improve the overall level of quality but reduce the cost of providing care as well.
“On the cost side, because we’ve been more efficient and we’ve tried to tease out unnecessary expense — and there are several buckets of expense, from labor to non-labor — we have reduced the cost per case by more than $1,100 from last November [2017] to this November,” he said. “And when you multiply that by the 1,400 or so discharges we had, that’s a savings of more than $1.5 million.”
With that, he went to his desk to retrieve the current average cost per discharge, $6,850, a number he had handy, and for a reason — it is carefully tracked, and its downward movement is a source of pride within the system.
It’s been accomplished through a number of means, he said, starting with staffing changes (none at the bedside) that result from consolidation in some areas, such as billing, that are made possible by synergies with the regional Trinity team, thus reducing overhead costs.
Further savings have been achieved on supplies, he said, returning to efforts to go paperless when possible, and also such things as travel expenses.
“We work with people; if they’re printing too much, we take steps to reduce that volume,” he said. “It doesn’t sound like much, but it adds up when you’re saving 50 cents or 75 cents on a print; it adds up over time. And it doesn’t contribute anything to patient care, so we’d rather put the money into patient care than into paper.”
As for travel, it has been cut back as well, he said, noting that meetings between the Mercy team and the system team are now staged electronically. “Instead of having our people drive to Hartford or their people drive here, we’re using technology,” he told HCN.
Huddling Up
As he offered a tour of the Mission Control room, Fulco started by referencing several large charts, called A3 charts, on the wall. Each one outlines an individual’s primary strategic aims, and they are part of the hospital’s lean daily management system.
“An A3 is putting our key objectives and measures all on one page,” he said, referencing his own A3, while noting that the charts track progress toward meeting those specific aims and goals, as laid out in an action plan. “We track this every week; we look at this every week. Every member of the leadership team has one of these.”
And when problems arise at those huddles, as he noted several times, everything is measured.
That goes for efforts to address recognized problems or issues as well, he went on, referring to other charts and the four letters ‘P,’ ‘D,’ ‘C,’ and ‘A,’ which stand for ‘plan,’ ‘do,’ ‘check,’ and ‘act,’ the four stages of tackling a problem, as Fulco identified them.
“This is flowing constantly; it’s changing every day,” he said, adding that the PDCA cycle, as it’s called, was created to generate action on a specific matter and keep things moving.
From Mission Control, the tour moved to the Patient Safety and Flow Room, where there was a comparatively small huddle going on (this was late afternoon). For the 8 a.m. huddles, those assembled have an agenda and start with safety, and move on to a daily operating summary and then performance reports — how well the hospital is doing with patient satisfaction, for example. Next is a round-robin session, at which feedback is sought on problems that have been identified.
But the tier 3 huddle is actually the second step in the process, said Fulco, noting that there are huddles on the departmental level as well. Matters arising at those sessions then come before the larger group, and there is then a Gemba walk. That’s a Japanese term that translates, loosely, into going to the front lines to see what’s going on, to hear from the people involved and come to understand the problem; it is similar in many ways to the concept known as MBWA — managing by walking around.
“A Gemba walk is daily rounding — we’re not sitting in our office or around a conference-room table; where going to see things where they really happen. We’re talking to people who are doing the work, and we’re doing some accountability checks,” said Fulco. “From 8:30 to 9:30 we take that walk, and from there we go to the Mission Control room and do an accountability huddle.
“It’s about getting close to the people,” he went on, “and finding out how we, as leaders, can help them.”
To emphasize these points, he concluded the tour in the Emergency Department, where are charts similar to those in both Mission Control and the Patient Safety and Flow Room.
They track things like wait times and numbers of patients who left without being seen — presumably because the wait times were too long — said Fulco, adding that subsequent huddles and PDCA charts identified the causes of those problems and tracked the success of steps taken to address them.
Healthy Outlook
Gemba walks. PDCA cycles. Huddles. A Mission Control room. These names, acronyms, and places all help explain how, while the mission hasn’t changed at Mercy Medical Center and Trinity Health Of New England, the process of carrying out that mission certainly has.
The emphasis today is on continuous improvement and being lean — without impacting the quality of care being provided at the bedside. As Fulco said repeatedly, in this environment, everything is measured, or charted, and progress is marked daily.
There is considerable work still to be done — this process never actually ends, he said — but progress can be seen in the ER, on the bottom line, and on the charts in the Patient Safety and Flow Room.
It could be seen as paper as well — only they’re using much less of it these days. That’s just part of the process of running lean. v
Comments are closed.